As a warehouse owner, balancing inventory management, overseeing operations, and maintaining a safe, efficient workforce can feel complex and overwhelming. As a result, a crucial element of warehouse security is often overlooked: the layout. A common misconception is that security is solely about installing surveillance cameras or alarm systems. While physical security measures are essential, a well-planned warehouse layout is equally as important when it comes to improving security.
In this article, we’ll explore key warehouse layout tips that can maximise your security and help to defend your assets.
Table of Contents
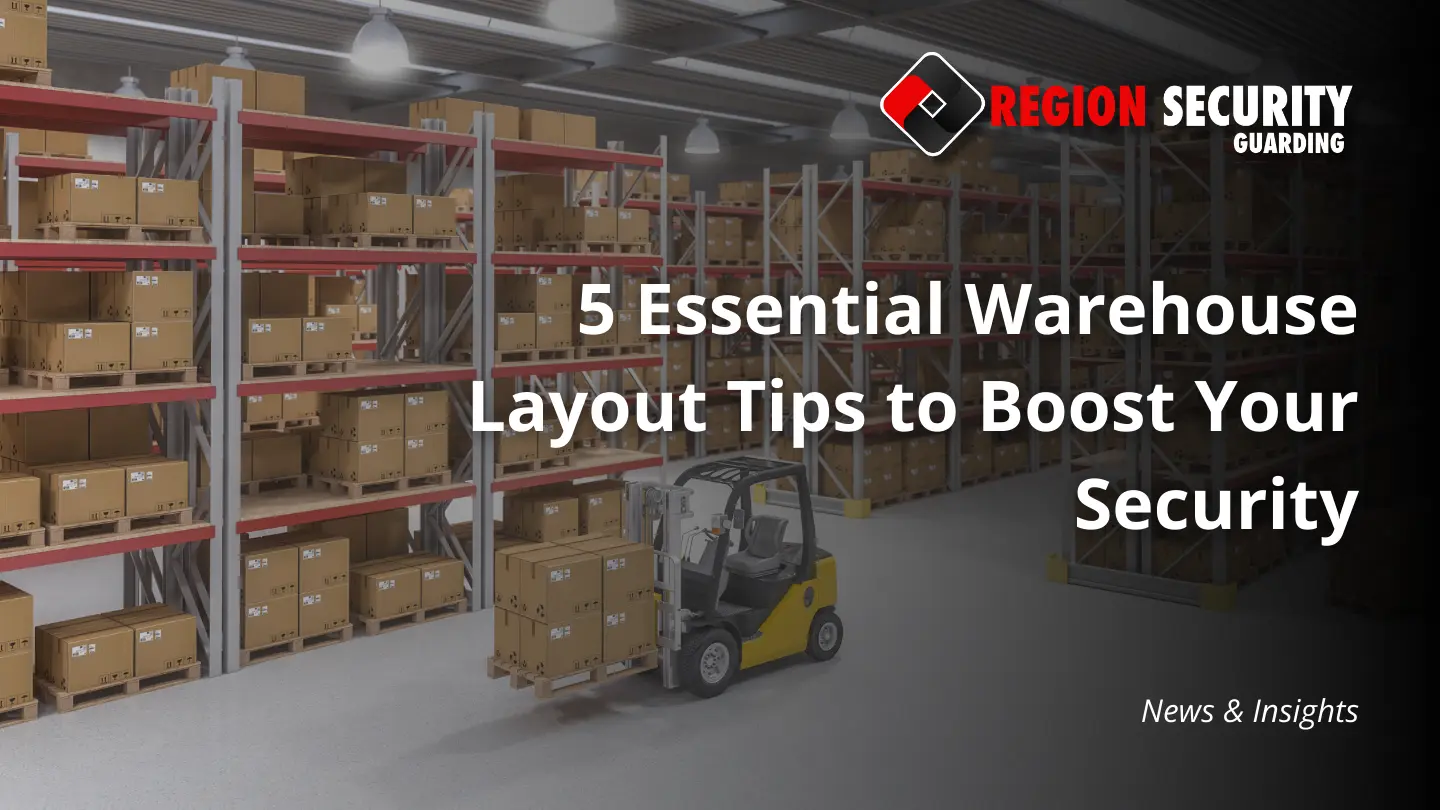
What is a Warehouse Layout?
The term “warehouse layout” refers to the physical arrangement of warehouse space, including storage areas, stock shelves, entry and exit points, loading docks, and the overall flow of goods. It also includes the placement of security infrastructure, such as cameras, alarms, barriers, and access control systems. A well-designed layout not only optimises space and improves workflow efficiency but is also crucial for ensuring operational and security effectiveness.
Why is Warehouse Layout Important for Security?
The layout of your warehouse directly impacts your ability to monitor and control access, reduce security risks, and prevent theft or accidents. A poor layout can create blind spots where criminal activity can go unnoticed or cause congestion that prevents security measures from functioning properly. On the other hand, an optimised layout enhances visibility, enables efficient movement of goods and personnel, and ensures high-risk areas are secured, all of which contribute to a more security environment.
What Are the Three Most Common Warehouse Layouts?
Before diving into warehouse layout tips for your space, it’s essential to understand the most common warehouse layout designs used in the industry. These designs can significantly influence how you structure your warehouse to maintain security.
The U-Shaped Layout
In this layout, the receiving and shipping areas are positioned next to each other, forming the ends of the “U.” Inventory storage forms the base of the “U,” arranged in a semi-circle. This arrangement allows goods to move efficiently from receiving to storage and then to shipping.
The I-Shaped Layout
This layout is the simplest of the three, involving a linear flow of goods, allowing you a good overview of your processes. Typically it allows for goods to easily travel from one end of the process to the other, starting with receiving to storage, then picking, and finally shipping. It’s a simple and efficient design, particularly useful for warehouses with straightforward, high-volume operations.
The L-Shaped Layout
In this layout, one end of the warehouse is dedicated to receiving and storage, while the other is used for picking and shipping. The L-shape offers good separation between receiving and shipping activities, improving efficiency and security potential for overviewing processes.
Warehouse Layout Tips to Improve Your Security
1. Secure Entry and Exit Points
Entry and exit points are the most vulnerable areas of your warehouse, often targeted by intruders or criminals seeking to steal inventory or cause damage. To reduce the risk of unauthorised access, it’s crucial to centralise these entry points, making them easier to track and monitor. By referencing the layout strategies of the three most common warehouse designs, positioning access points at the ends of the warehouse can create a more efficient and secure system.
For added security, access control systems such as key cards can be installed at these points. Barriers like gates and fences can further restrict unauthorised entry, while security guards can verify the identities of visitors to ensure only approved personnel are allowed access.
2. Clear Sightlines for Better Visibility
A cluttered warehouse with limited visibility can lead to accidents, such as theft, or make escape difficult during an emergency. To address this, create open spaces by organising shelving and storage systems to eliminate blind spots. Prioritise vertical storage to maximise space and keep aisles clear. Position aisles and workstations in open areas to ensure visibility, enhancing workplace safety.
Structuring your layout this way is essential for creating a safer warehouse environment, as it enables security guards and CCTV cameras to be positioned at strategic vantage points for rapid threat detection. Improved visibility not only strengthens security but also acts as a deterrent to potential intruders while reassuring employees that their safety is being actively monitored.
3. Segregate High-Value Goods
Warehouses often store high-value inventory, making them prime targets for theft and necessitating stronger security measures. To reduce the risk, designate specific zones for storing high-value items, ideally placing them further from access points. Positioning them towards the middle or back of the warehouse makes them significantly harder to reach and steal from.
In addition to strategic placement, ensure these zones or shelves are physically secured. If necessary, install gates or locks around them, or deploy security guards and additional cameras to provide an extra layer of surveillance.
4. Secure Loading and Unloading Zones
Loading and unloading zones are common targets for security breaches. Unprotected or poorly designed loading docks can provide easy access for criminals to steal goods or gain unauthorised entry to the warehouse. To mitigate this risk, ensure these areas are visible from multiple points within the warehouse, particularly by security guards and surveillance systems.
Strategically positioning these zones at the ends of the warehouse makes them easier to monitor and enhances their visibility. Keep the surrounding areas clear and open to maintain unobstructed sightlines, allowing for better detection of potential intruders.
5. Install Proper Lighting
Poorly lit warehouses can encourage criminal activity, as intruders are less likely to be seen in dimly lit areas. To reduce this risk, install motion-activated lights at key locations, such as entrances, exits, and the perimeter. In areas where consistent visibility is crucial, use bright, uniform lighting to eliminate dark corners and blind spots.
Outdoor lighting is equally important. Floodlights around the exterior of the warehouse, along the perimeter, and at access points serve as a visible deterrent to intruders. Consider using LED lights for their energy efficiency and long lifespan.
Conclusion
Integrating these essential warehouse layout strategies into your security plan will help protect your warehouse, assets, and employees. A well-designed layout, combined with professional security personnel and additional security measures, creates a strong defence against theft, accidents, and other risks. Warehouse owners who prioritise both layout improvements and strengthening their security ensure a safer and more efficient working environment.
By optimising layout, access points, surveillance, and emergency procedures, you can take proactive steps to safeguard your business. Contact our team today to learn how we can help you strengthen your warehouse security and create a safer workplace for your team and assets.
Business Security You Can Rely On
Trusted by leading businesses nationwide for reliable, 24/7 protection.
or call 0330 912 2033
We have used Region security for quite a while now. Top notch service, great guards and helpful staff. We love our guards and the team for all of their help / work. No need to try the other companies at all."
Andy Yeomans - Jones Skips Ltd
Great company, professional services, friendly guards and helpful at times when required."
Rob Pell - Site Manager
A professional and reliable service. Always easy to contact and has never let us down with cover. No hesitation in recommending and competitively priced also. After using an unreliable costly company for several years it is a pleasure to do business with Region Security"
Jane Meier - Manager
Region Security were very helpful in providing security for our building. We had overnight security for around 4 months. The guards themselves were professional, easy to reach and adapted very well to our specific needs. Would definitely recommend Region for security needs.
Lambert Smith Hampton
Great service. Reliable and professional and our lovely security guard Hussein was so helpful, friendly but assertive with patients when needed. He quickly became a part of our team and we would love to keep him! Will definitely use this company again
East Trees Health Centre
Fantastic Service from start to finish with helpful, polite accommodating staff, we have used Region Security a few times now and always been happy with what they provide.
Leah Ramsden - Manager